POWERCOAT PRO
- Excellent gloss and long-life properties
- Long lasting “easy-to-clean” coating
- Old and bleached surfaces “freshened up” as new
- Protection against UV rays prevents bleaching of surfaces
- “Anti-Graffiti” and “Anti-fingerprinting” finish
- Long lasting protection against corrosion.
- Abrasion resistant
- Stability against condensation and climatic/temperature variations
- Resistance against acid and solvent attack
- No special preparation of the base material required
- High productivity because of extremely thin coating thickness
POWERCOAT PRO™
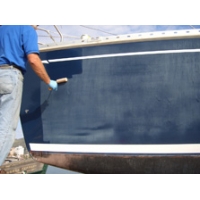
With coverage nearing 100sq.mtrs per litre, Powercoat Pro offers exceptional gloss retention and weather resistance for many years. Probably the most versatile and long-lasting nanocoating on the market today, it is perfect for use on aluminium, stainless-steel, brass, copper, magnesium, ceramics, GFK glass-fibre, plastics, concrete, as well as on plaster surfaces, hardwood and mineral bases. In fact, it can be applied to almost any surface except glass to protect against anything the environment might throw at it! Even surfaces already coated with other products can be “refreshed”, sealed and protected on a long-term basis.
Sealed surfaces are able to be easily cleaned without using a special cleanser and are more resistant to new soiling by virtue of Powercoat Pro’s “easy-to-clean” effect. Dull and tired paintwork, chalky glass-fibre (GFK) surfaces and cloudy and tired anodised aluminium gleams again “just like new” and in their original colours after treatment. Galvanised surfaces such as aluminium, brass, copper, and chrome are protected long-term against corrosion. Due to the extremely thin nature of the coating – just 5-20microns – a coating capacity of about 70m² – 100m² per 1kg can be achieved on non-absorbent surfaces. Despite being so thin, however, the coating is highly resistant to all kinds of chemical attacks and extreme weathering.
Nanolia’s Powercoat Pro is a two-component clear coating based on chemical nanotechnology that is highly effective against graffiti. Defacement by, for example, felt-tip pens is resisted and simply “pearls-off”. Highly adhesive paints can be easily removed using Nanolia AG REMOVAL LIQUID or GEL.
NB: Powercoat Pro copolymer coating complies with Title 21, Code of Federal Regulations, Chapter 1, part 177.2600 for use in articles intended for repeated contact with food.
It has also passed Australian Water Industry tests to AS/NZS 4020:2005 for
- Odour and flavour of water in contact with the material
- Appearance of water in contact with the material
- Mutagenic activity of water in contact with the material
- Growth of aquatic micro-organisms on the material
- Cytotoxicity
- Extraction of metals.
Note: For application to concrete or plastered surfaces we are able to offer a less glossy version. We recommend for colouring the use of an acrylic emulsion undercoat. Used on such surfaces 30 – 40 m² can be achieved with 1kg. Details are in a separate data sheet, GRAFFITI GUARD FOR NON-POROUS SURFACES.
Technical Data: |
|
Mixing proportions: |
Base : Hardener 5.5 : 1 by weight or volume |
Dilution: |
Do not dilute |
Finish: |
High gloss |
Color: |
transparent |
Coating thickness: |
5 – 20 µm (dry) |
Temperature Stability: |
-40 °C to +350 °C |
Pot-Life: |
About 4 hours (at 20 °C) |
Dust Dry:* |
After about 6 hours * (at 20 Degr. C) |
Finally Dry: * |
After about 7 days * (at 20 Degr. C) |
Second Coating: |
Not necessary |
Accelerated Drying: |
Above 60 °C (when dust-dry) |
HVLP: |
Nozzle 0,8 mm. Pressure 2,0 bar |
*Working at a temperature below 15 degrees can result in a much longer drying time. |
Always test a small sample to ensure that the desired result is achieved before proceeding with the main project. Note that this product has a long curing time and that the test sample should be left for at least 24 hours before checking. If in doubt, do not proceed.
The base surface to be treated must be thoroughly cleaned, dry and free from fat/oil, and also free of any silicone, wax or polish traces using Nanolia PreCleaner. Pre-treatment with Acetone is not sufficient. For Aluminium and Magnesium surfaces Nanolia Pre-Clean M1 is recommended. No prior priming is required. Nanolia’s Powercoat Pro coating can be used on surfaces that have already been painted with other products, as a sealing. Coatings must be thoroughly dry (minimum drying period of 6 weeks), and before application a test should be made on the surface to be treated in a suitable place. Any areas of corrosion which may be present must be removed. If used for the coating of plastic materials a test should be made in a suitable place to test that the base material has enough resistance to solvents. (i.e. decorative stripes on the boat hull). The adhesion on glassfibre GFK and on plastic materials is improved, in certain cases, by prior sanding with a very fine sandpaper.
Use undiluted. Please note that the mixing proportions are calculated by weight or volume and must be strictly adhered to. The smaller the amount required, the more exact must be the quantities of the components. When mixing the base component and the hardener, according to the volume instructions, it is vitally important that separate dosing nozzles are used for the base component and the hardener. Never dip the nozzle which has been used to take up the base material immediately into the hardener and vice-versa. Should even the smallest amount of the base component get into the hardener, it is possible that the hardening component chemically “turns” and is no longer useable. Close the container with the hardening component immediately after extracting the amount you need. After adding the hardening agent it is advisable to let the mixture rest for about 15 minutes, in order that the air bubbles caused by mixing can escape.
The maximum pot-life of the mixed components is 4 hours – therefore please make sure that you mix no more of the product than you require in this time span. Although the mixed product may still be liquid after a period of 24 hours, it is not to be used after the pot-life period of time.
The working temperature (both the working environment and the base material) to be treated must be above 5 °C. The best results are to be achieved at between 15 °C and 25 °C. Do not work with the product in direct sunlight. High air humidity following the application accelerates the drying.
Application is possible using the accepted methods (rolling, brush-painting, spraying or by immersion). To achieve the most successful surface HVLP-Spray application is recommended. Alternatively you can apply with a fine pored foam roller (use strong pressure in order get a really thin surface without stripes or dimples) or a lint free cloth (only for small surfaces recommended). Apply to the surface, as thinly as possible. It is a basic principle of application that “less is more”. The very best results are obtained when the coating is applied wafer-thin on the surface to be treated. Due to the lengthened drying time, it is possible to polish out any foreign bodies from the coating. A treated surface cannot be painted over. A second coating should only be applied after a light sanding-down.
After use the working tools may be cleaned with the usual thinners available locally. If you use dosing squirts for mixing: The one used for the base material can be used several times; but the one for hardener should be cleaned each time with water.
Following the correct application, the shine/gloss, smoothness and hardness are not immediately finally apparent, but in the course of the following few days become more and more visible.
Details in the application vary depending upon the surface which is to be coated. We are happy to advise you fully in these cases.
0.5 kg bottles, 5 kg canister, 10 kg canister, 25 kg hobbock. Other packing forms/sizes are possible after prior consultation with us and according to the transport possibilities/regulations.
The product may be stored for at least 12 months in its original packing. Protect from frost and direct sunlight.
Empty containers as well as any remaining product must be disposed of according to the local laws and regulations or it must be taken to the community collection point for such materials.
When using this product please take note of these instructions. We wish to make it clear that the use of chemical preparations should only take place when the safety measures are observed and are always out of the reach of children. The technical information given here is according to the latest technical knowledge and composed from our own experience. In view of the many uses possible with this product it is therefore the responsibility of the user to act according to the given situation in respect of safety – that is to say the user acts upon their own responsibility in any given situation when using this product. That the use of this product takes place out of our jurisdiction, we have set out safety and protection measures, but we cannot be held responsible in any circumstances. For any misuse of the product we cannot be held responsible. In the event of a new version of this information becoming available – this information here set out is no longer valid.